As a consumer, we are primarily concerned with the things that directly impact the day-to-day performance of a vehicle: battery capacity, power output, energy efficiency, and temperature management. However, more complicated testing happens before batteries make it to consumers. This testing is both essential and required by law. Many organizations exist today to verify compliance with safety standards, environmental regulations, and performance requirements, including organizations such as International Electrotechnical Commission (IEC), Society of Automotive Engineers (SAE), and Underwriters Laboratories (UL).
Battery testing can be broken into two major parts:
- Pre-consumer design validation and manufacturing - verify that the battery system meets the specified requirements and functions as intended under various operating conditions
- Consumer - verify that the battery system continues to perform as desired, mainly in terms of performance and longevity
Pre-Consumer Testing
Although drivers, owners, and shoppers are usually focused on the consumer side testing, we’ll run through the testing that happens before the batteries even make their way into a car. This testing plays a critical role in identifying any design flaws, manufacturing defects, or deviations from quality standards. The data gathered from these tests helps manufacturers refine the battery design, enhance manufacturing processes, and ensure that only reliable and safe batteries reach the market.
Design Validation and Manufacturing Stage
Design Validation Stage
- Performance: Evaluating the battery's capacity, power output, and energy efficiency using tests such as charge and discharge cycles.
- Environmental: Evaluating their performance and safety under extreme environmental conditions (e.g. high/low temperatures, humidity, thermal shock, and vibration).
- Safety: Evaluating safety features like overcharging protection, thermal runaway prevention, and crashworthiness.
- Lifetime and Aging: Accelerated aging tests to assess long-term performance and degradation, specifically around factors like capacity loss, internal resistance increase, and voltage stability.
Manufacturing Stage
- Quality Control: Ensure consistency, identify defects, and validate adherence to quality standards via cell-to-cell variations, electrical integrity, and proper assembly of battery components.
- Safety Compliance: Ensuring that batteries comply with international safety standards in regards to safety features, electrical insulation, protection circuits, and resistance to external hazards.
- Performance Validation: Capacity testing, power output verification, and impedance measurements.
- End-of-Line: Functional tests, performance assessments, and safety checks to validate that each battery unit meets the defined standards.

Consumer Stage
All the above testing happens before a battery makes it into a car, and generally, it is an effective process to weed out defects and design flaws. However, once a battery is in use, it becomes much harder for a driver, owner, or buyer to get information about its health and performance.
Testing an EV battery typically requires specialized equipment and expertise. While professionals or battery testing laboratories can run comprehensive tests like the ones above, there are a few basic steps you can take to assess the performance of your EV battery.
It's important to note that while these basic tests can provide some insights into the performance of your EV battery, they may not cover all aspects of comprehensive battery testing. Read more about why it’s so difficult to get even basic stats about batteries.
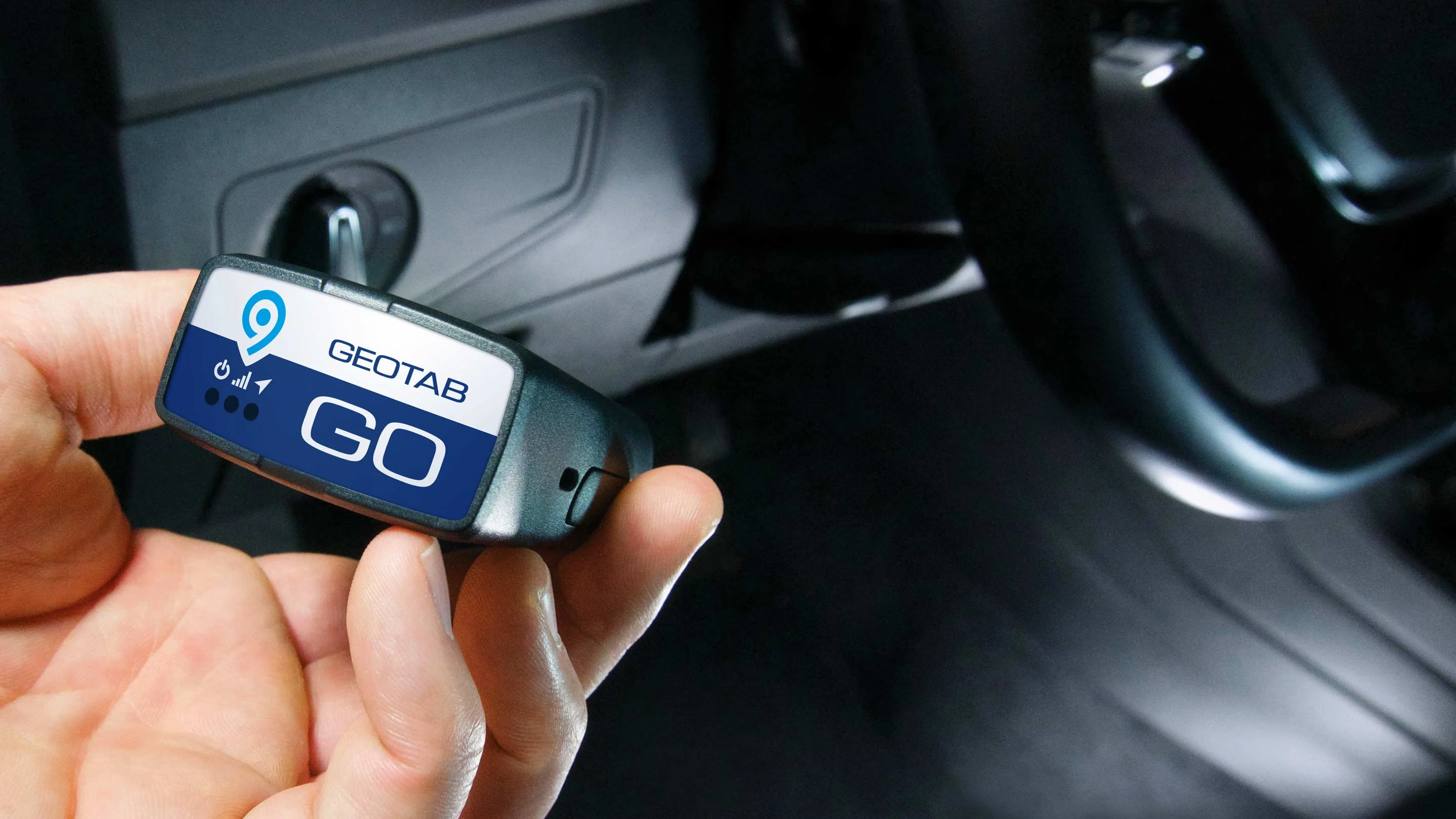
Basic testing
- Battery Capacity: One of the simplest ways to test the battery is to charge the car for a specific amount of time, then compare the change in battery percentage to the change in battery capacity (SOC). If we add 33 kWh to a Chevrolet Bolt battery that is 66 kWh in size, we should see a SOC change of 50% (i.e. 10% to 60% or 40% to 90%). Testing a variety of ranges is ideal to ensure the BMS is capable of accurately determining various battery percentages, and that the battery is receiving the amount of energy that we expect.
- EV Range: Although an EVs range can greatly depend on driving conditions, including driving style, temperature, and terrain, monitoring the vehicle’s range compared to EPA estimates and historical data for your specific vehicle can provide insights into the battery health.
- State of Health (SOH): Many EVs provide a built-in battery health monitoring system, which is controlled via the BMS. Generally, accessing this information requires an on-board diagnostic device (OBDII reader), which taps into the BMS to provide quantitative data such as battery temperature, battery voltage, and SOH.
- Software Solutions: If you’re trying to get information about the battery of an EV that you already own or have access to, there are a lot of consumer-side software tools that can help. These tools use data from your car to give nuanced evaluations of battery health. Many are brand-specific, such as Tessie or TeslaFi for Tesla, or LeafSpy for LEAF. Recurrent Reports are a great option for most EVs on the road today, and are free to drivers and shoppers.
Advanced testing
Modern EV batteries are usually integrated in parallel or in modules to boost the capacity and driving range. These modules are then grouped in series to form the packs, allowing the battery to meet the high voltage demand.
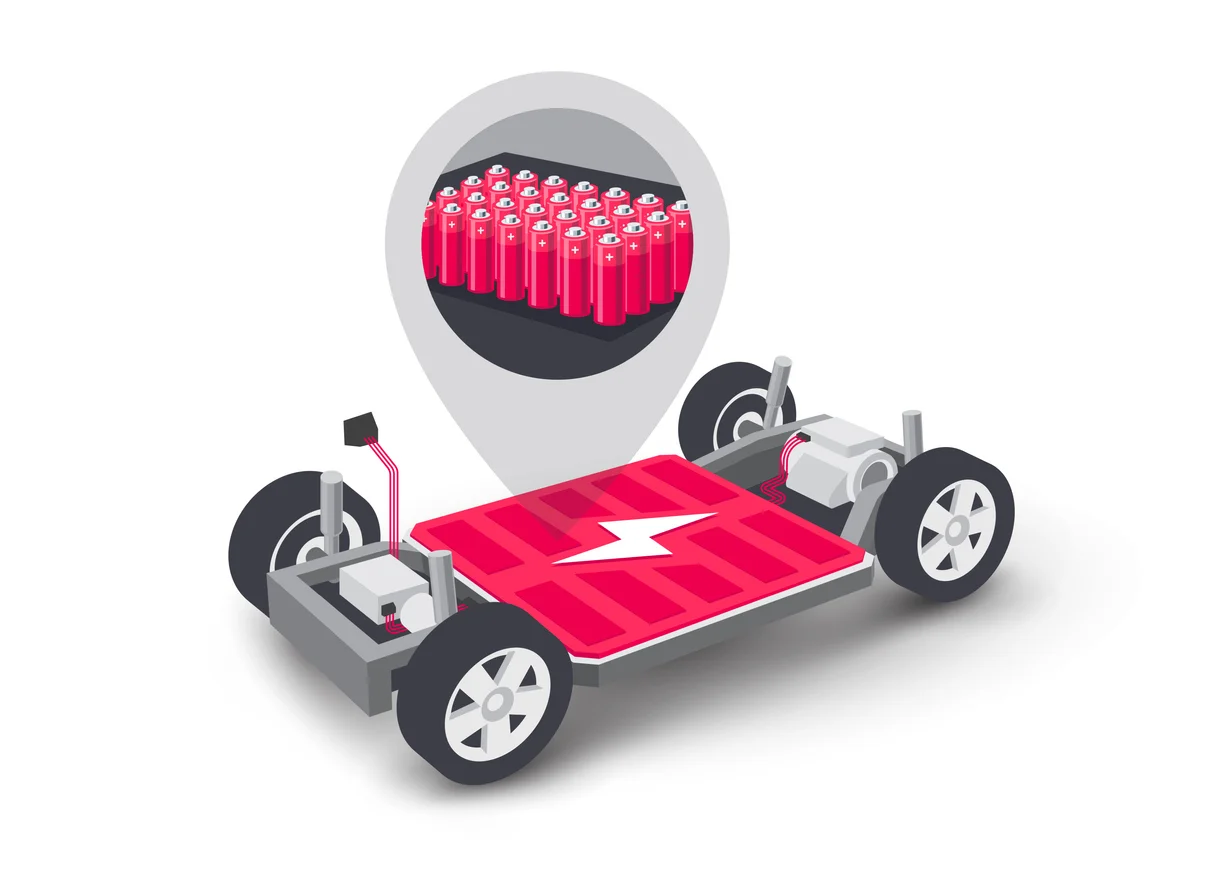
Historically, battery SOH measurement has been focused on single cells, rather than modules or at the pack level. In practice, an EV battery replacement is necessary when capacity drops below 70%. The overall capacity measurement is driven by the weakest battery in the pack, so one failing module may trigger a warning that all of the batteries in the pack have reached end of life. This is a significant drawback of the complex organization of series and parallel connections that make up a battery pack. The internal resistance within the pack or module is also impacted by small differences between cells, providing another element of complexity in SOH measurements. Several methodologies exist today that can assess battery health at the pack level and can accurately replicate the actual SOH of the individual cells.
- Impedance-based: Electrochemical-impedance spectroscopy (EIS) utilizes the electrochemical processes occurring within the battery. Specifically, this method measures the impedance within the battery - the opposition to electrical flow - at multiple frequencies to analyze the behavior of the electrode-electrolyte interfaces. Although this method requires little time, the reliability of the EIS is sensitive and highly dependent on battery pack size, state of charge, and temperature. Additionally, EIS requires expensive electronics with significant post-processing, making its implementation difficult.
- Static capacity: This includes methods such as incremental capacity analysis (ICA), differential voltage analysis (DVA), and differential thermal voltammetry. These methods are far more simple than EIS and require less expensive equipment, since they rely on the characterisation of battery capacity and internal resistance. Several studies have confirmed that changes in the internal capacity curve can be used as an indication of capacity fade in a battery module pack that has parallel-connected cells, similar to results obtained when measuring individual cells.
Unfortunately, studies have indicated that while both diagnostic methods were effective in detecting abnormalities for packs placed in series, the methods struggled to discover similar abnormalities within parallel modules (read more about battery configurations).
To bypass shortcomings related to specific battery architecture, several thermal monitoring techniques have been developed. These methods involve using sensors and thermal imaging cameras to measure temperature distribution across the battery. By monitoring temperature variations and identifying hotspots, thermal monitoring helps assess thermal management, a key component used to evaluate potential safety risks and battery health.
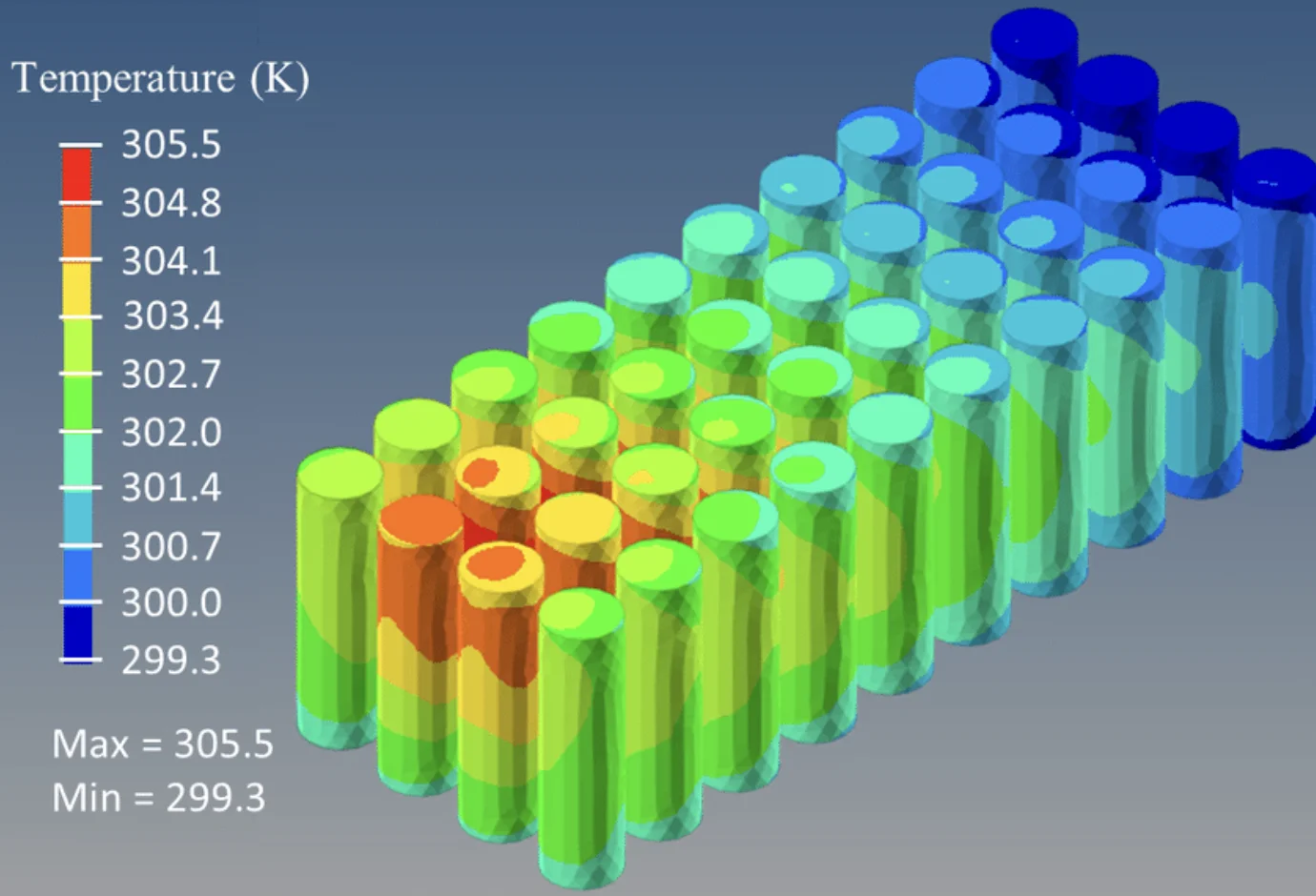
The average capacity of EV batteries is expected to continue to increase as technology in the lithium space expands. However, as EV adoption increases, so does the number of lithium-ion batteries, and although these batteries are typically longer-lived compared to alternatives, they possess a finite lifetime. Increased market growth and average EV age means that the number of batteries reaching the end-of-life stage will soon increase dramatically. The sourcing, production, and recycling of EV batteries is therefore extremely important to the ecological, economic, and social impact that they will make. Proper battery testing protocols are essential for both manufacturers and consumers to ensure that EV adoption and use is done in a responsible manner.