How to Accelerate Electrification
Electrification requires contributions from many groups, including automobile manufacturers, battery miners and manufacturers, charging companies, and grid operators. As the transition picks up steam, ongoing battery advancements are essential in order to:
- decrease costs
- increase range and safety, and
- reduce the environmental impact.
The majority of EVs today are powered by lithium-ion batteries, a technology that has been around for decades in consumer devices such as laptops and smartphones. Improvements in battery chemistry and battery management systems have allowed the production of vehicles that can travel 300+ miles, charge in 30 minutes, and cost only slightly more than a gas powered alternative.
However, there is still room of improvement.
What are the major roadblocks with current battery technology?
There are three main factors that improved battery technology is looking to address:
- Increased capacity - the more energy a battery can hold, the higher range it has, the less it needs to be recharged, and theoretically - the lower the range anxiety for reluctant or anxious customers. However, with current technology, increased capacity means more vehicle weight. The holy grail is to be able to increase capacity without just adding in more of the same, heavy, battery cells.
- Increased charging rates - if you have a small battery, but recharging takes no longer than filling up a gas tank, then maybe your battery capacity doesn't matter so much! This is the thinking behind teams working to improve charge rates. The issue with faster charging today is that it hinges on high voltage and high amperage, which may damage current battery cells over time. Plus, super fast chargers require a lot of electric infrastructure to deliver a high powered charge.
- Reduced costs - Even if an electric vehicle has a limited battery capacity and requires 20-30 minutes to recharge, if it is cheap enough, people will buy ‘em. Cost reduction in battery technology tries to address the supply constraints around key minerals, as well as the environmental and socioeconomic costs associated with mining them.
Some of the key innovations for the next iteration of batteries include next-generation cathode and anodes, sodium-ion technology, and solid-state batteries. In the following sections, we will break down the current state of each of these technologies, specifically addressing improvements to current battery technology in cycle life, charging rates, and safety.
Solid-State Batteries
A traditional lithium-ion battery is composed of cathode, anode, separator, and electrolyte.
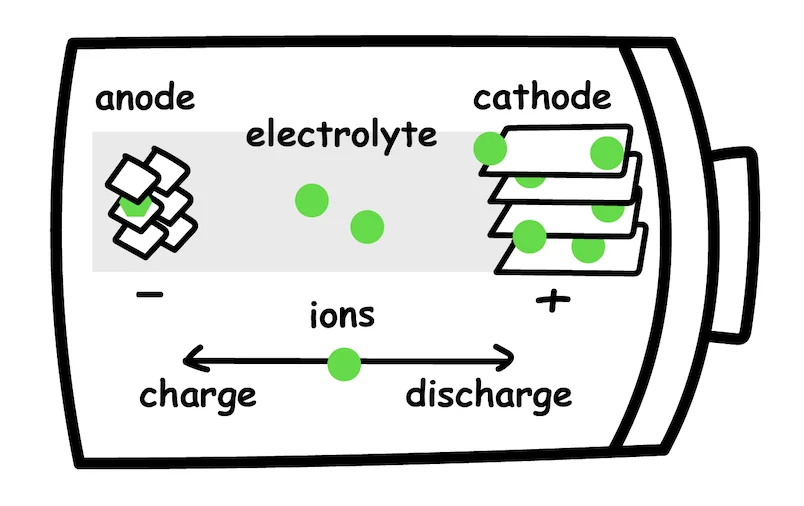
Current lithium-ion batteries use a liquid electrolyte that shuttles charge around, helping to generate a current to propel the vehicle forward. In a solid-state battery, this liquid solution is replaced with ceramics or other solid materials.
Why would we favor a solid over a liquid? If you think back to thermodynamics, you might remember that liquids expand and contract more than solids. As a result, a liquid-based electrolyte, which swells and contracts as the battery is in use, has a higher risk of damage or leakage. Additionally, replacing the liquid, organic separator with a non-flammable, non-combustible solid-state one significantly reduces the risk of fire.
While safety is an important consideration to manufacturers and governments, the average consumer is likely to care about vehicle function: namely range and charge rates.
Increasing battery capacity
Theoretically, the largest increase in range can be achieved by increasing the number of batteries or increasing the size of the battery, both of which are costly and require additional space and weight. The next best option is to increase the energy density of the battery, or how much energy a battery can store per unit of space. Energy density is a function of battery chemistry.
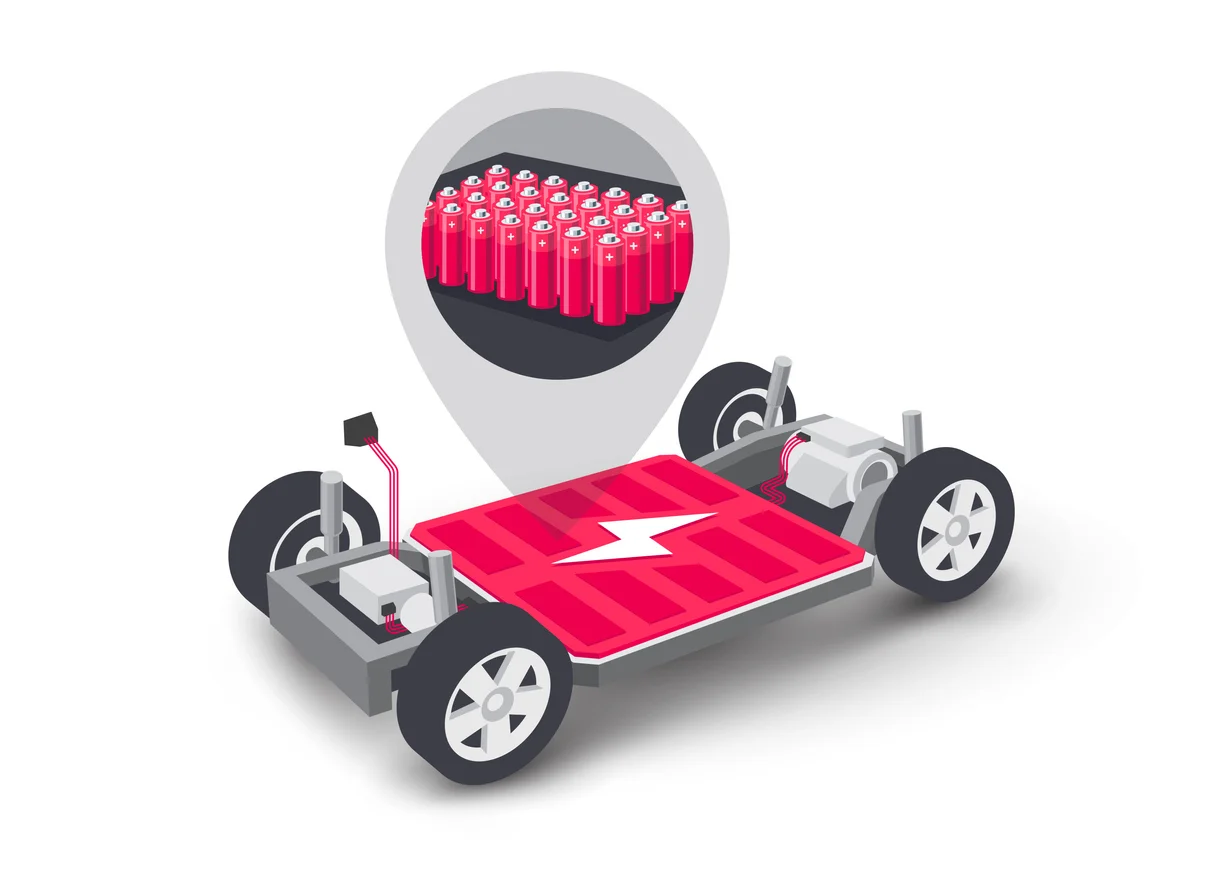
For example, previous generation EV batteries, such as the lead-acid battery pioneered by Toyota, have an energy density of 30-50 Wh/kg. Lithium-ion batteries, on the other hand, can have an energy density of 150-200 Wh/kg, which makes them more able to carry more energy in smaller spaces, and thus more useful for portable applications. Recent studies suggest solid-state batteries may have an energy density 2-2.5 times greater than current lithium-ion technology.
Increasing charge rate
Maximum charging rates have improved drastically over the years, ranging from 50 kW in a Chevrolet Bolt to 300+ kW in vehicles such as the Kia EV6. Although this technology is still quite young, it seems possible that solid state batteries could one day achieve charging rates up to six times faster than current batteries. This could mean charging from 10% to 80% in 5 minutes!
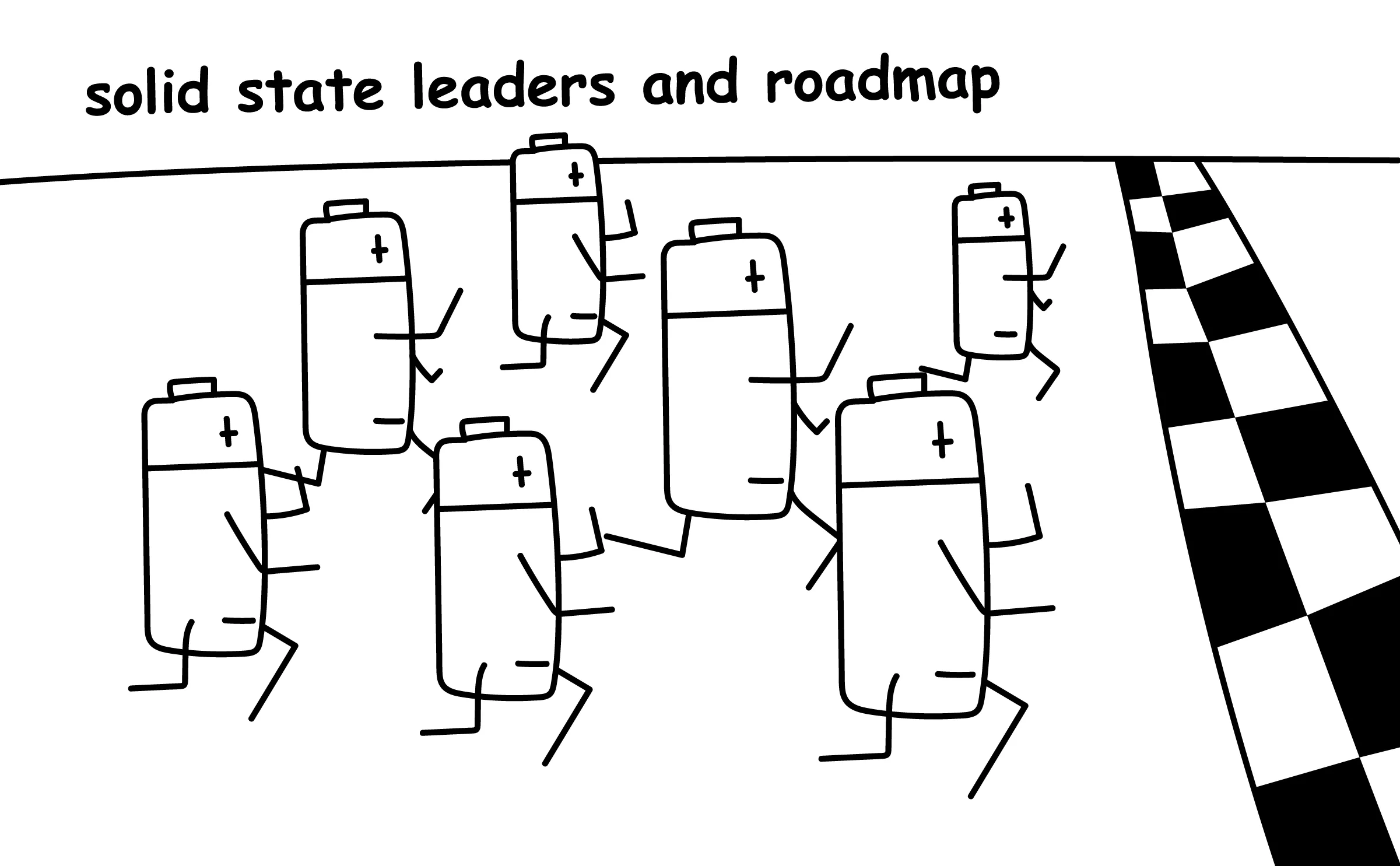
Solid State: Where things stand
Despite the promising future for these batteries, solid electrolytes are still in the early stages of development. Here are some of the particular challenges associated with this technology:
- Components may shrink and swell during charge and transport, which may alter the performance and health of the system through delamination at the interfaces.
- Solid electrolytes are made of brittle materials, which may break under pressure. How does this translate to car crashes, for instance?
- Increased energy density can mean higher pressure in a battery. Will solid state batteries need next generation anodes to support the added pressure?
- Costs are still relatively high compared to standard lithium-ion batteries.
Researchers around the world, such as the Department of Energy’s Oak Ridge National Laboratory, are working towards better understanding the mechanics involved in battery performance. Mechanical influences, such as stress and strain through pressure and heat, are known to affect the performance of a battery, but the specific impacts on battery efficacy and longevity are not fully understood. But, things seem promising: several years ago, the Samsung Advanced Institute of Technology published data indicating a solid-state battery could be discharged over 1000 times, meaning potentially improved output, life cycle and safety - all in a smaller package.
When it comes to solid-state battery testing and production, companies such as QuantumScape and Solid Power are at the cutting edge. Both expect prototype batteries to be delivered to manufacturers such as VW, Ford, and BMW in 2024 or 2025. Realistically, this puts the timeline for mass produced solid-state batteries much closer to 2027 to 2028. Along the same lines, Toyota recently announced breakthroughs to the company's solid-state lithium-ion batteries, claiming a greater tolerance for high voltage and temperature, meaning that their cells will allow for rapid charging and discharging. The downside for the Toyota batteries is a noticeably shorter life. Toyota expects solid-state batteries to be ready for commercial use by 2027-2028 in next-generation EVs, although they plan to initially introduce the technology in hybrid vehicles.
Next Generation Anodes
A typical battery is composed of two nodes - formally called electrodes - that are separated by a substance that allows ions to move between them. Like other components of a battery, the specific material choices of the anode will affect the safety, charging speed, capacity, and life cycle. The anode, or the negatively charged electrode, is often made of graphite, and more specifically, synthetic graphite, which is a graphitic carbon generated from very high temperatures.
As with other key battery elements, graphite is sourced through a tight supply chain. While the production of synthetic graphite can be cheaper than natural graphite, it depends on fossil fuels and large amounts of energy, often leading to hefty associated greenhouse gas emissions. Manufacturers and environmental groups would like to reduce the anode’s carbon footprint while simultaneously increasing energy density. Silicon anode research has emerged at the forefront of this research.
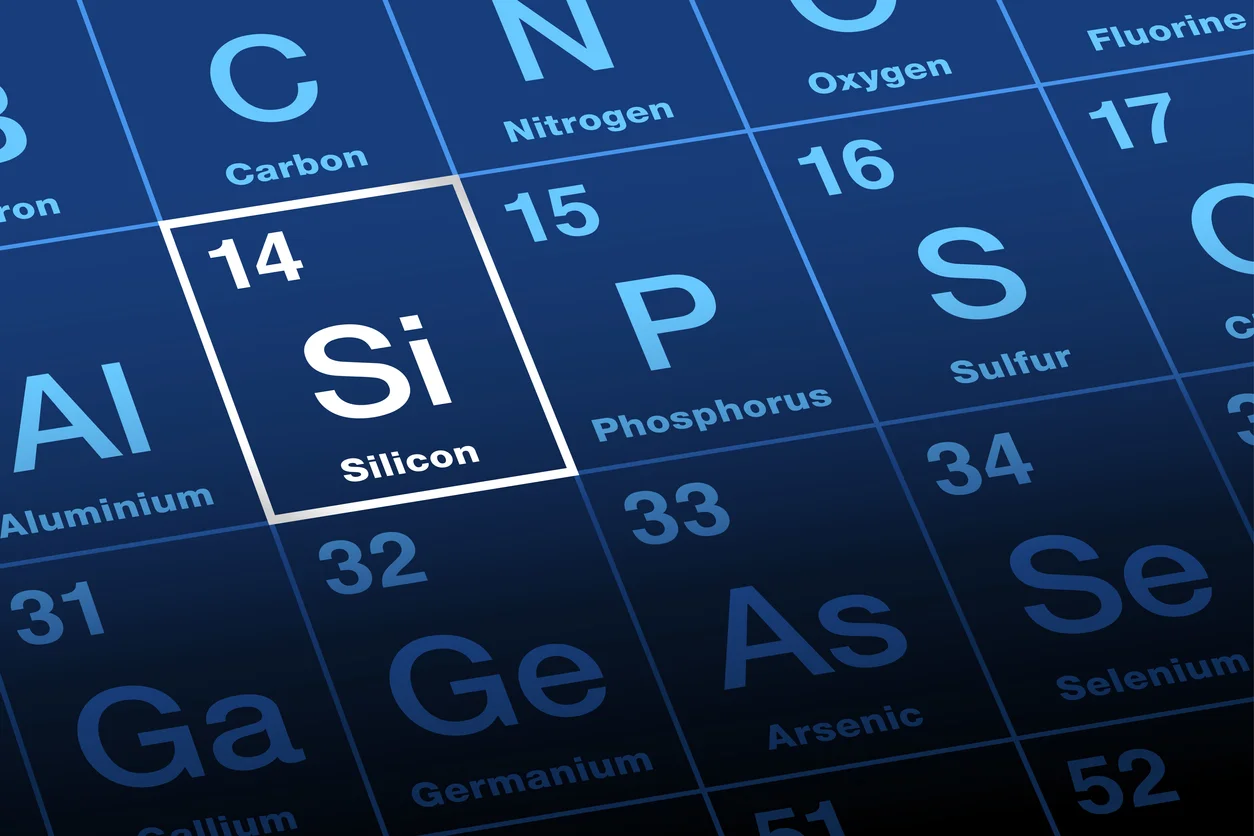
GM reported using silicon in electrochemical cells nearly a decade before the first use of a graphite anode. However, silicon was quickly overshadowed by graphite, which was almost immediately commercialized in the early 1990s. Why? Unfortunately, silicon has two properties that make it hard to use at scale. First, it tends to expand its volume during the alloy process, making it unsuitable for the stress of ongoing electrochemical reactions. Additionally, pure silicon anodes have high reactivity with other chemicals, meaning that they will have a lot of secondary, waste reactions with other chemicals in the battery. In short, these properties hinder its use at the commercial level.
Research in the mid-1990s, around the time that graphite anodes were really taking off, demonstrated that nano-sized silicon integrated into carbon structures might offer a solution to silicon’s drawbacks. It wasn’t until the early 2000s that this new branch of structural engineering really took off, with several startups emerging with the goal of commercializing silicon-based anodes.
One such startup, Sila Nanotechnologies Inc., claimed that using “refined silicon materials known as nano-composite silicon reduces the weight of cells, improves battery range and shortens charging time.” This means that nano-silicon battery cells might hit on some of the three main development goals. Lighter weight cells mean that less energy is needed to move a car. Improved battery range and faster charge speeds address consumer issues. And, making silicon-based anodes may address some industry concerns about the environmental and carbon costs of making batteries.
In mid-2022, Mercedes announced a partnership with Sila to incorporate their silicon-based anodes by mid-decade. Similarly, GM recently partnered with OneD Battery Sciences to incorporate silicon anodes into GM’s Ultium battery cells, which can be found in the newly released Chevrolet Blazer EV and Equinox EV.
Sodium Batteries
Lithium is an abundant material, but difficult to extract for use in batteries. Additionally, recent headlines have emphasized the environmental and socioeconomic impacts of lithium mining. Sodium is a chemically similar element that is also quite abundant, but significantly cheaper and associated with fewer environmental problems. As a result, many groups are interested in producing sodium-based batteries to reduce costs and carbon footprint.
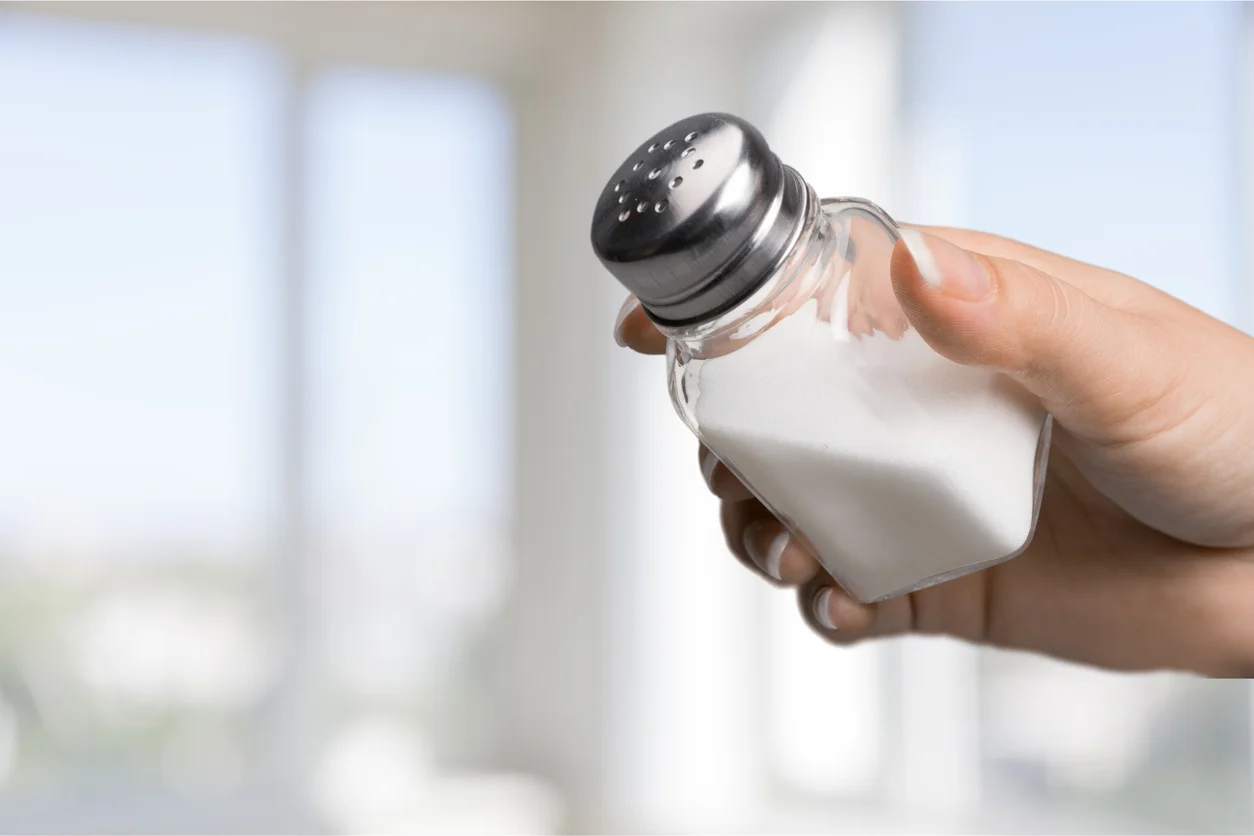
Despite sodium being chemically similar to lithium, sodium-ion batteries have considerably lower energy density than lithium-ion batteries, which is a major drawback for widespread adoption, especially when it comes to passenger vehicles. However, a major plus for sodium batteries is that they are less sensitive to low temperatures than their lithium-ion cousins. Additionally, initial studies indicate that sodium-ion batteries may be more resistant to charge/discharge degradation, improving cycle life.
It’s unlikely that sodium-ion batteries will replace lithium-ion batteries, but there’s a strong chance that they will be used for certain applications where high energy density isn’t necessary (e.g. grid storage). At the very minimum, production of sodium-ion batteries, or integration of sodium-ion cells into primarily lithium-based batteries, may help alleviate the pressure associated with obtaining some of the raw materials and the supply chain risks that come with pure lithium-ion batteries.
To this end, two Chinese companies, CATL and BYD, both plan on producing battery packs that have a mix of sodium-ion and lithium-ion cells. The rationale for mixing the two is that sodium cells help with low temperature performance, and lithium cells help with standard performance. In fact, the majority of sodium battery factories are located in China, and experts expect that within two years, China will have ~95% of the world’s capacity to make sodium batteries.
In addition to the decreased energy density that sodium-ion batteries offer, several other drawbacks are worth considering.
- Sodium-ion batteries often contain toxic materials such as vanadium.
- Given their low-cost, recycling sodium batteries may not be profitable. This will make it harder to ensure eco-friendly end-of-life treatment.
- Interactions between sodium ions and specific materials requires the use of non-standard cathodes, but little is known to date regarding the effects of such chemical reactions.
Some of the issues associated with pure sodium-ion batteries can be solved with next generation anodes and cathodes, mixing lithium-ion cells with sodium-ion cells, and moving towards solid-state battery architecture. At this point, the jury is still out on the efficacy and safety of sodium-ion batteries, with many laboratories and industry leaders working towards revealing those answers. Given that it’s not clear whether these batteries will be able to meet needs of EVs in the transportation sector, several companies, such as US-based Natron, are starting with less-demanding applications such as energy storage and small-scale transportation (i.e. e-bikes, scooters).
Other Technologies
Despite numerous emerging technologies, the lithium-ion battery is still the most prevalent battery chemistry for EVs and is unlikely to be replaced in the short-term. Therefore, many groups are still interested in improving lithium-based batteries by improving the underlying technology. One such improvement might be by changing the chemistry used in the cathode.
Currently, cathodes are composed of of layered transition metal oxides, such as:
- Lithium cobalt oxide (LCO)
- Lithium nickel cobalt manganese oxide (NMC)
- Lithium nickel cobalt aluminum oxide (NCA)
These formulations are chosen due to their high energy densities and long cycle lives. Unfortunately, these compounds contain materials such as cobalt and nickel, both of which are expensive, toxic, and are difficult to obtain. If these cathodes could be replaced by sustainable, high energy density chemistries, some of the lifecycle and environmental costs could be reduced.
Disordered Rock Salt
One research field is cation-disordered rock-salt, which has attracted attention based on its ability to improve battery capacity and compositional flexibility, decoupling the need for controversial metals such as cobalt and nickel. More specifically, replacement of cathodes based on cobalt and nickel with metals such as manganese, iron, and vanadium-based cathodes has significantly improved redox reactions, resulting in much higher energy densities. Although current production methods are time and energy intensive, and hence expensive, several groups have recently devised new methods to synthesize the rock salt compounds. This improves the likelihood that these cathodes will be integrated into existing lithium-ion batteries.
Zinc-Air Batteries
Zinc-based batteries are one of the oldest energy-storage systems. Zinc-air batteries use a zinc (metal) anode and oxygen as active material in the cathode. Historically, these batteries were not cost effective due to expensive components. However, researchers at Sydney University in Australia previously demonstrated the feasibility of a zinc-air battery for EV application, demonstrating high energy density, low environmental impact, low cost, and improved safety. EnZinc, an engineering company based out of California, is one company working towards commercializing zinc-air batteries through the production of their zinc microsponge anode technology. EnZinc’s goal is to "reduce EV battery cost by more than 50%, double the amount of energy stored, and allow for greater rechargeability.”
NanoBolt Lithium Tungsten
In an attempt to improve the underlying features of the already useful lithium-ion battery, researchers have added tungsten and carbon nanotubes to the anodes of existing batteries. The inclusion of these structures provides increased surface area for ion transfer, which allows for faster ion movement, increasing rates of charge and discharge. Additionally, the battery has the ability to hold greater charge compared to traditional designs, with little compromise. Such batteries are being designed and produced by large companies including N1 Technologies, CALT, LG Energy Solution, and Nyobolt.
Any other cool battery technology on your radar? Drop us a line contact@recurrentauto.com